This case study demonstrates the implementation of SEA Vision's Harleblister and Databox solutions on a pharmaceutical blister packaging line. Integrated into a Marchesini INTEGRA320 blister and cartoning machine, the solution enhanced product quality and packaging accuracy through:
✅ Blister completeness checks,
✅ Tablet correctness inspection,
✅ Alucode verification,
✅ OCV on lidding foil,
✅ Data matrix verification on leaflets,
✅ Pharmacode checks on cartons.
The integration of these advanced inspection technologies ensured compliance with stringent international pharmaceutical standards while improving operational efficiency.
Read the full case study⬇️
Challenge
Key challenges in pharmaceutical blister packaging included:
-
Blister Completeness and Tablet Correctness: Ensuring each blister is correctly filled.
-
Alucode Verification: Confirming the accuracy and alignment of printed codes on sealing foil.
-
OCV on Lidding Foil: Verifying variable data such as batch numbers and expiry dates.
-
Data Matrix Verification on Leaflets: Checking the non-serialized data matrix on leaflets for accuracy.
-
Pharmacode Verification on Cartons: Ensuring pharmacodes on carton flaps match product specifications.
Manual inspection was insufficient due to high production volumes and data complexity. A fully automated solution was required to eliminate errors, ensure compliance, and maintain operational efficiency.
Solution
SEA Vision implemented the Harleblister and Databox systems integrated with the Marchesini INTEGRA320 line, delivering comprehensive inspection capabilities:
1. Blister Completeness and Tablet Correctness (Harleblister):
Cameras inspected each blister to verify presence and correctness of tablets, rejecting any with errors.
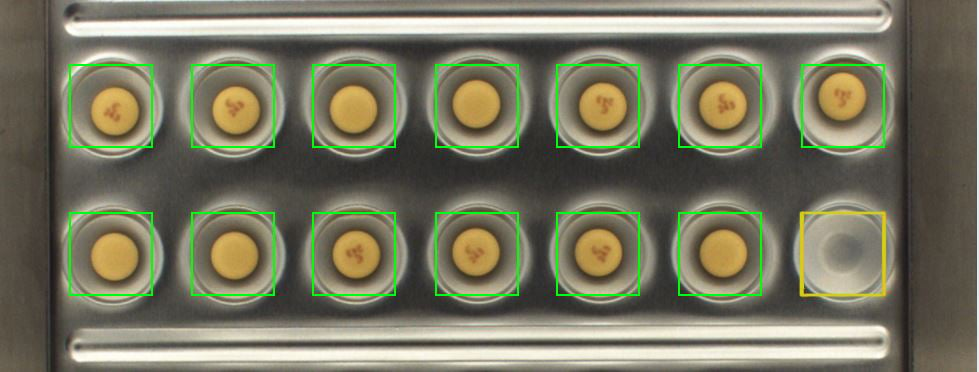
2. Foil and Data Verification (Harleblister):
Dedicated cameras checked the Alucode for accuracy and alignment and performed OCV checks on batch numbers and expiry dates.3. Data Matrix Verification on Leaflets (Databox):
Verified the data matrix code on leaflets, triggering rejection of non-compliant cartons.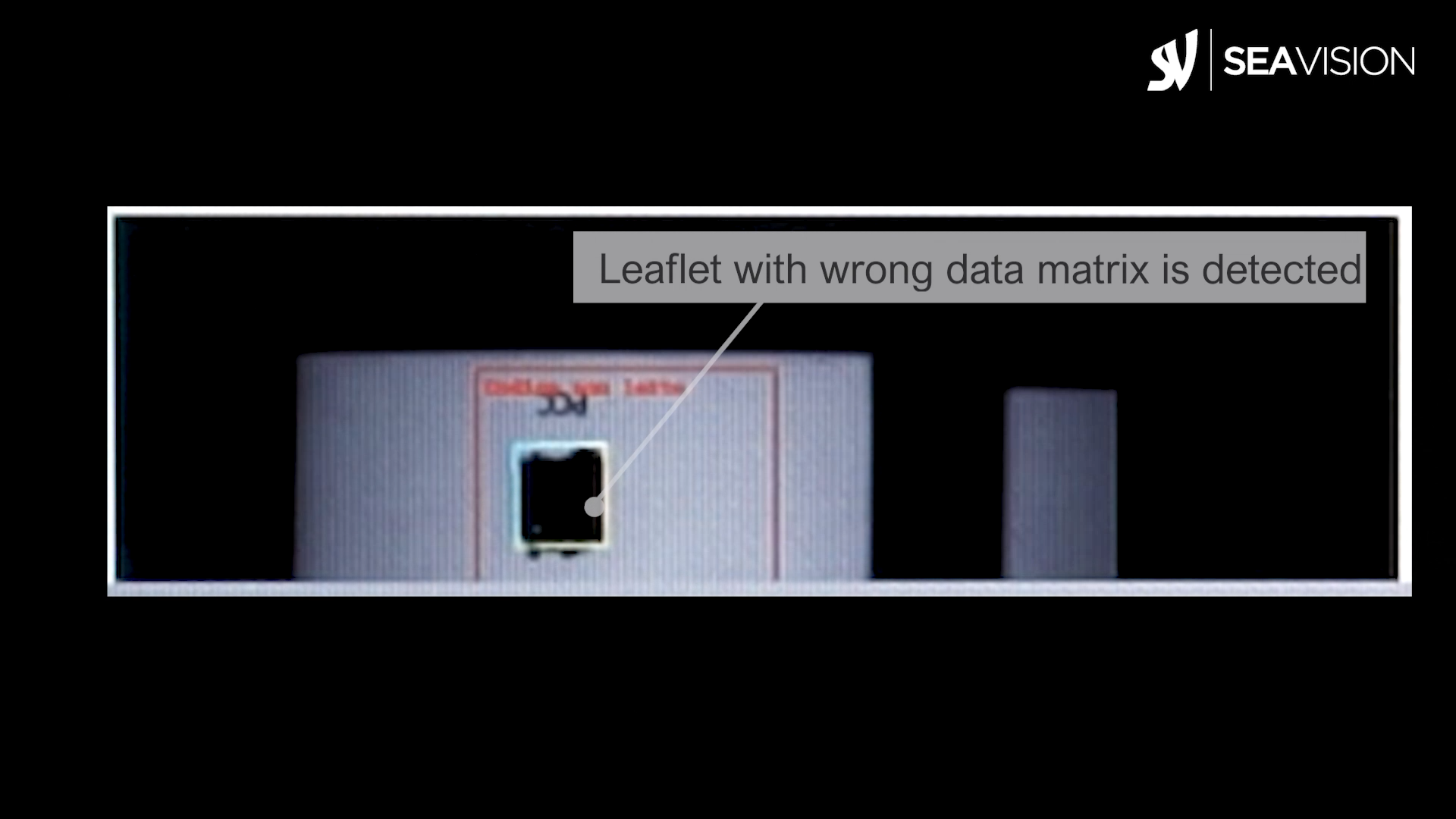
4. Pharmacode Verification on Cartons (Databox):
Checked pharmacodes on carton flaps to ensure correct product identification.These systems integrated with the OEM’s HMI to provide real-time data and control for operators.
Results
The implementation delivered key benefits:
-
Enhanced Quality Control: Automated inspections reduced error risks across packaging stages.
-
Operational Efficiency: High throughput was maintained without compromising quality.
-
Regulatory Compliance: Ensured compliance with pharmaceutical packaging and labeling standards.
-
Flexibility and Integration: Seamless HMI integration enabled comprehensive operator control and monitoring.
Other Applications
The adoption of SEA Vision's Harleblister and Databox solutions significantly improved product quality and packaging efficiency for this pharmaceutical packaging line. Automating the inspection process reduced errors and ensured compliance with international regulatory standards, demonstrating the critical role of advanced vision inspection systems in modern pharmaceutical manufacturing.
Learn More
For further information about SEA Vision's Track & Trace solution and Marchesini Group’s MC820 case packer, visit: